Main principles of pumps selection
The selection of the pumping equipment is a crucial point that determines both process parameters and the in-use performance of the unit under development. During the selection of the type of pump three groups of criteria can be distinguished:
- Process and design requirements
- Nature of pumped medium
- Key design parameters
Process and design requirements:
In some cases, the pump selection is determined by some stringent requirements for a number of design or process parameters. Unlike piston-type pumps, centrifugal pumps can provide uniform delivery of pumped medium, whereas in order to meet uniformity condition on a piston-type pump its design has to be made noticeably complicated, by arranging on the crankshaft several pistons making reciprocating movements with certain delay from each other. At the same time, delivery of pumped medium in discrete portions of set volume can also be a process requirement. An example of definitive design requirements can be the use of submerged pumps in cases when it is necessary and only possible to install the pump below the level of the pumped fluid.
The pump process and design requirements are seldom definitive, and ranges of suitable types of pumps for various specific cases of application are known as a matter of experience accumulated by humanity, and there is no need to enumerate them in detail.
Nature of pumped medium:
Characteristics of the pumped medium often become a decisive factor in pumping equipment selection. Different types of pumps are suitable for pumping of various media differing in viscosity, toxicity, abrasiveness and many other parameters. So screw pumps can pump viscous media with different inclusions without damaging the structure of the medium, and can successfully be used in the food-processing industry for pumping of jams and pastes with various fillers. Corrosion properties of the pumped medium determine the material design of the selected pump, and toxicity – degree of its air-tightness.
Key design parameters of pumps
Regardless of the diversity of machines used for pumping of fluids and gases, a number of key parameters defining their functioning: capacity, power consumption and head can be singled out.
Capacity (delivery, flow rate) – the volume of medium pumped by a pump per unit of time. It is denoted by the letter Q and has dimensions in m3/h, l/s, etc. Flow rate quantity includes the only factual volume of displaced fluid ignoring return leakages. The theoretical and factual flow rate ratio is expressed by volumetric efficiency quantity:
But in modern pumps thanks to reliable sealing of pipelines and joints the factual capacity coincides with theoretical. In the majority of cases, a pump is selected for the particular pipeline system and the flow rate value is set in advance.
Head – energy imparted by pump to the pumped medium and attributed to unit of pumped medium mass. It is denoted by the letter H and has dimensions in meters. It should be clarified that the head is not geometrical characteristic and is not the height to which a pump can lift pumped medium.
Power consumption (shaft power) – power consumed by pump during operation. Power consumption differs from pump useful capacity consumed directly for imparting of energy to the pumped medium. Part of consumed power can be lost due to leakages, bearings friction, etc. Performance factor determines ratio between these quantities.
Calculation of these characteristic may vary for different types of pumps, which is associated with differences in their design and operating principles.
Calculation of performance capacity for different pumps
The entire diversity of types of pumps can be divided into two main groups with calculation of performance capacity having fundamental distinctions. By operating principle the pumps are subdivided into nonpositive displacement and positive displacement pumps. In the first case medium is pumped due to dynamic forces that influence it, and in the latter case – through variation of volume of pump operating chamber.
Nonpositive displacement pumps include:
1) Friction pumps (vortex, auger-type, disk, jet pumps, etc)
2) Impeller pumps (axial-flow, centrifugal)
3) Electromagnetic pumps
Positive displacement pumps include:
1) Reciprocating pumps (piston and plunger, diaphragm pumps)
2) Rotary pumps
3) Impeller pumps
Piston pumps (positive displacement pumps)
The main operating component of the piston pump is cylinder in which piston is moving. The piston reciprocates by means of crank mechanism, thus providing consistent variation of operating chamber volume. In one complete turn of crank from the endpoint the piston makes full-forward stroke (discharge) and reverse stroke (suction). During discharge in cylinder the piston creates overpressure, under the action of which suction valve opens and discharge valve closes, and fluid being pumped is delivered to the delivery pipeline. During suction reverse process takes place, during which vacuum is created in cylinder through piston backward movement; discharge valve closes preventing return flow of pumped fluid, and suction valve opens and cylinder is filled through it. Real performance capacity of piston pumps is somewhat different from theoretical, which is related to a number of factors, such as fluid leakages, degassing of gases dissolved in pumped fluids, delays in opening and closing of valves, etc.
For single-acting piston pump the flow rate formula will look like the following:
Q = F·S·n·ηV
Q – flow rate (m3/s)
F – piston cross-sectional area, m2
S –piston stroke length, m
n – shaft rotation speed, s-1
ηV – volumetric efficiency
For double-acting piston pump performance capacity arithmetic formula will look slightly different, which is related to availability of piston rod reducing the volume of one of the cylinder operating chambers.
Q = F·S·n + (F-f)·S·n = (2F-f)·S·n
Q – flow rate (m3/s)
F – piston cross-sectional area, m2
f – rod cross-sectional area, m2
S – piston stroke length, m
n – shaft rotation speed, s -1
ηV – volumetric efficiency
With neglect of rod volume, general formula of piston pump performance capacity will look in the following way:
Q = N·F·S·n·ηV
where N – number of actions made in one shaft revolution.
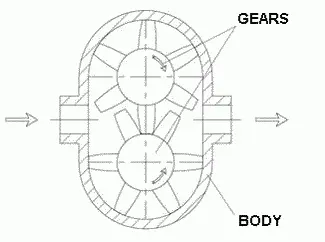
Gear pumps (positive displacement pumps)
Gear pumps
In case of gear pumps role of the operating chamber is performed by space limited by two adjacent teeth of gear. Two gears with internal or external engagement are installed inside the body. Pumped medium is sucked into the pump by vacuum created between gears teeth going out of engagement. Teeth transfer fluid inside pump body, and then it is squeezed to discharge pipe at the time when teeth engage again. For flow of pumped fluid the gear pumps are provided with end and tooth tip clearances between body and gears.
Gear pump performance capacity can be calculated in the following way:
Q = 2·f·z·n·b·ηV
Q – gear pump performance capacity, m3/s
f – cross-sectional area of space between adjacent gear teeth, m2
z – number of gear teeth
b – gear tooth length, m
n – teeth rotation speed, s-1
ηV – volumetric efficiency
There is also an alternative formula for calculation of gear pump performance capacity:
Q = 2·π·DН·m·b·n·ηV
Q – gear pump performance capacity, m3/s
DН – gear pitch diameter,m
m – pitch of a gear, m
b – gear width, m
n – gear rotation speed, s-1
η – V – volumetric efficiency
Screw pumps (positive displacement pumps)
Screw pumps
In pumps of this type medium is pumped by means of screw operation (single-screw pump), or several screws being in engagement, if the question is of multiscrew pumps. Profile of screws is selected in a way for the pump injection zone to be isolated from the suction zone. The screws are mounted inside the body in such way that during their operation enclosed space zones filled with pumped medium were formed limited by outline of screws and body, and moving towards injection zone.
Single-screw pump performance capacity can be calculated in the following way:
Q = 4·e·D·T·n·ηV
Q – screw pump performance capacity, m3/s
e – eccentricity, m
D – diameter of rotor screw, m
Т – pitch of stator screw surface, m
n – rotor rotation speed, s-1
ηV – volumetric efficiency
Centrifugal pumps
Centrifugal pumps are one of the most numerous representatives of nonpositive displacement pumps that are widely used. The working member of centrifugal pumps is put on shaft impeller provided with blades enclosed between disks and mounted inside spiral-shaped body.
Impeller rotation creates centrifugal force affecting the mass of pumped media inside the impeller, and imparts to it part of kinetic energy passing then into potential energy of head. When this happens the vacuum created in the impeller provides continuous delivery of pumped medium from suction pipe. It is important to note that before starting operation the centrifugal pump should be first filled with the pumped medium, as otherwise suction force will not be sufficient for proper pump operation.
Centrifugal pump may have not one working mechanism, but several. In this case the pump is called multistage. In terms of design it is distinguished by having several impellers on the shaft at a time, and fluid successively passes through each of them. Having one and the same performance capacity the multistage pump will create greater head as against single-stage pump analogous to it.
Centrifugal pump performance capacity can be calculated in the following way:
Q = b1·(π·D1-δ·Z)·c1 = b2·(π·D2-δ·Z)·c2
Q – centrifugal pump performance capacity, m3/s
b1,2 – widths of impeller pass through diameters D1 and D2,m
D1,2 – inlet external diameter (1) and impeller external diameter(2), m
δ –thickness of blades, m
Z – number of blades
C1,2 – radial components of absolute velocities at impeller inlet (1) and its outlet (2), m/s
Calculation of head
As it was stated above, the head is not geometrical characteristic and can not be identified with height to which pumped fluid has to be lifted. The required head value is composed of several summands, with each of them having its own physical sense.
General formula of head calculation (diameters of suction and discharge pipes are taken as equal):
H = (p2-p1)/(ρ·g) + Hг + hп
H – head, m
p1 – intake tank pressure, Pa
p2 – receiving tank pressure, Pa
ρ – density of the pumped medium, kg/m3
g – gravity acceleration, m/s2
Hг – geometrical height of the pumped medium lift, m
hп – head overall loss, m
The first of summands of head calculation formula represents drop of pressures which should be overcome in the process fluid pumping. Occasionally, pressures p1 and p2 may coincide, with head created by pump spent on lifting fluid to certain height and overcoming the resistance.
The second summand characterizes geometrical height to which the pumped fluid has to be lifted. It is important to note that during determination of this quantity geometry of pressure pipeline which may have several lifts and falls is not taken into account.
The third summand characterizes drop of created head depending on characteristics of the pipeline through which medium is pumped. Real pipelines will inevitably exhibit resistance to fluid flow. In order to surmount it one needs to have head margin. Total resistance is composed of pipeline friction losses and losses due to local resistances, like pipe turns and branches, gate valves, passage widening and contraction, etc. Overall pipeline head losses are calculated by the formula:
Hоб = HТ + HМС = (λ·l)/dэ·[w2/(2·g)] + ∑ζМС·[w2/(2·g)] = ((λ·l)/dэ + ∑ζМС)·[w2/(2·g)]
Hоб – head overall losses made up of pipe friction losses Hт and local resistance losses Нмс
λ – friction coefficient
l – pipeline length, m
dЭ – pipeline equivalent diameter, m
w – flow rate, m/s
g – gravity acceleration, m/s2
[w²2/(2·g)] – velocity head, m
∑ζМС – sum of all coefficients of local resistances
Calculation of pump power consumption
Several kinds of power are singled out according to transmission losses taken into account by different efficiency coefficients. Power spent directly on transmission of pumped fluid energy is calculated by the formula:
NП = ρ·g·Q·H
NП – useful power, W
ρ – density of the pumped medium, kg/m3
g – gravity acceleration, m/s2
Q – flow rate, m3/s
H – total head, m
Power developed on pump shaft is larger than the useful one, and its excess is consumed for compensation of pump power losses. Interrelation between useful power and shaft power is set by pump efficiency. The pump efficiency includes leakages through seals and openings (volumetric efficiency), losses of head while pumped medium is flowing inside pump (hydraulic efficiency), and friction losses between moving parts of the pump, such as bearings and glands (mechanical efficiency).
NВ = NП/ηН
NВ – power on pump shaft, W
NП – useful power, W
ηН – pump efficiency
In its turn, power developed by motor exceeds the shaft power, which is necessary to compensate for energy losses in its transmission from motor to pump. Electric motor power and shaft power are linked by efficiencies of transmission and motor.
NД = NВ/(ηП·ηД)
NД – motor power consumption, W
NВ – shaft power, W
ηП – transmission efficiency
ηН – motor efficiency
Final motor generating capacity is calculated from motor power with regard to potential overload during start up.
NУ = β·NД
NУ – motor generating capacity, W
NД – motor power consumption, W
β – power safety margin
Power safety margin can be tentatively selected from the table below:
N, kW Under 1 From 1 to 5 from 5 to 50 Over 50
β 2 – 1.5 1.5 – 1.2 1.2 – 1.15 1.1
Extreme suction head (for centrifugal pump)
Centrifugal pump suction occurs due to pressure differential between vessel from which pumped medium is taken, and impeller blades. Excessive increase of pressure differential may result in the occurrence of cavitation – process when pressure drops down to value at which fluid boiling temperature lowers below pumped medium temperature and it starts to evaporate in flow space forming multiple bubbles. Bubbles are carried away by stream further downstream where under action of building up pressure they are condensed and collapse, accompanied with multiple hydraulic shocks that negatively tell on pump service life. In order to avoid negative influence of cavitation the suction head of centrifugal pump has to be limited.
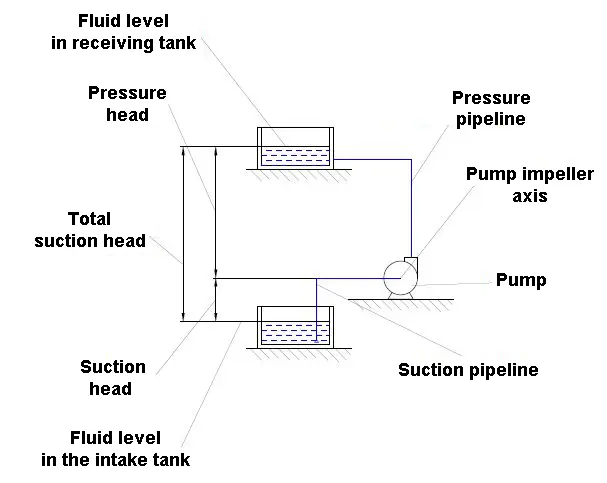
Geometric suction head can be determined by the formula:
hг = (P0-P1)/(ρ·g) - hсв - w²/(2·g) - σ·H
hГ – geometric suction head, m
P0 – intake tank pressure, Pa
P1 – pressure of the impeller blades, Pa
ρ – pumped medium density, kg/m3
g – gravity acceleration, m/s2
hсв – losses due to overcoming suction pipeline hydraulic resistance, m
w²/(2·g) – suction pipeline velocity head, m
σ*H – added resistance losses proportional to head, m
where σ – cavitation factor, H – head created by pump
Cavitation factor can be calculated by the empirical formula:
σ = [(n·√Q) / (126H4/3)]4/3
σ – cavitation factor
n – impeller rotation speed, s-1
Q – pump performance capacity, m3/s
Н – created head, m
There is also formula for centrifugal pumps for calculation of head margin providing absence of cavitation:
Hкв = 0,3·(Q·n²)2/3
Hкв – head margin, m
Q – centrifugal pump performance capacity, m3/s
n – impeller rotation speed, s -1
Examples of problems and solutions for calculation and selection of pumps:
Example No. 1
Single-action plunger pump provides pumped medium flow rate of 1 m3/h. Plunger diameter is 10 cm, and stroke length is 24 cm. Working shaft rotation speed is 40 rpm.
The pump volumetric efficiency has to be found.
Solution:
Plunger cross-sectional area:
F = (π·d²)/4 = (3,14·0,1²)/4 = 0,00785 m²2
Efficiency is expressed from the formula of plunger pump flow rate:
ηV = Q/(F·S·n) = 1/(0,00785·0,24·40) · 60/3600 = 0,88
Example No. 2
Double-action two-piston pump creates head of 160 m in pumping oil having density 920 kg/m3. Piston diameter is 8 cm, rod diameter – 1 cm, and piston stroke length equals to 16 cm. Working shaft rotation speed equals to 85 rpm. It is necessary to calculate required power of electric motor (pump and electric motor efficiency should be taken as 0.95, and adjusting coefficient 1.1).
Solution:
Cross-sectional areas of piston and rod are:
F = (3,14·0,08²)/4 = 0,005024 m²
F = (3,14·0,01²)/4 = 0,0000785 m²
Pump performance capacity is found by the formula:
Q = N·(2F-f)·S·n = 2·(2·0,005024-0,0000785)·0,16·85/60 = 0,0045195 m³/h
Then we find pump useful power:
NП = 920·9,81·0,0045195·160 = 6526,3 W
Taken into account efficiency and adjusting coefficient we obtain final installed power:
NУСТ = 6526,3/(0,95·0,95)·1,1 = 7954,5 W = 7,95 kW
Example No. 3
Three-piston pump is pumping fluid with density of 1,080 kg/m3 from open tank to vessel under pressure 1.6 bar with flow rate of 2.2 m3/hour. Geometric head of fluid lift is 3.2 meters. Useful power consumed for fluid pumping is 4 kW. Value of head loss has to be found.
Solution:
We find head created by pump from the formula of useful power:
H = NП/(ρ·g·Q) = 4000/(1080·9,81·2,2)·3600 = 617,8 m
We substitute found head value in the formula of the head expressed in difference of pressures, and find sought quantity
hп = H - (p2-p1)/(ρ·g) - Hг = 617,8 - ((1,6-1)·105)/(1080·9,81) - 3,2 = 69,6 m
Example No 4
Real screw pipe performance capacity is 1.6 m3/h. Pump geometrical characteristics are: eccentricity – 2 cm; rotor diameter – 7 cm; pitch of rotor screw surface – 14 cm. Rotor rotation speed equals to 15 rpm. Pump volumetric efficiency has to be found.
Solution:
We express sought quantity from the formula of screw pump performance capacity
ηV = Q/(4·e·D·T·n) = 1,6/(4·0,02·0,07·0,14·15) · 60/3600 = 0,85
Example No 5
It’s necessary to calculate head, flow rate and useful power of centrifugal pump pumping low-viscosity fluid with density of 1,020 kg /m3 from tank with overpressure 1.2 bar to tank with overpressure 2.5 bar along given pipeline with pipe diameter 20 cm. Total pipeline length (summarily with equivalent length of local resistances) equals to 78 m (friction coefficient is accepted as equal to 0.032). Difference of reservoirs heads is 8 meters.
Solution:
For low-viscosity media we select optimal movement velocity in pipeline equal to 2 m/s. We calculate fluid flow rate through set pipeline:
Q = (π·d²) / 4·w = (3,14·0,2²) / 4·2 = 0,0628 m³/s
Pipe velocity head is:
w²/(2·g) = 2²/(2·9,81) = 0,204 m
At corresponding velocity head friction and local resistances losses will equal:
HТ = (λ·l)/dэ · [w²/(2g)] = (0,032·78)/0,2 · 0,204 = 2,54 m
Total head will equal:
H = (p2-p1)/(ρ·g) + Hг + hп = ((2,5-1,2)·105)/(1020·9,81) + 8 + 2,54 = 23,53 m
Useful power is left to be determined:
NП = ρ·g·Q·H = 1020·9,81·0,0628·23,53 = 14786 W
Example No 6
Is it reasonable to pump water by centrifugal pump having performance capacity of 50 m3/h through 150 х 4.5 mm pipeline?
Solution:
We calculate velocity of water flow in the pipeline:
Q = (π·d²)/4·w
w = (4·Q)/(π·d²) = (4·50)/(3,14·0,141²) · 1/3600 = 0,89 m/s
Velocity for water flow in delivery pipeline equals to 1.5-3 m/s. Value of flow velocity thus obtained does not fall within this interval, wherefrom one may conclude that the use of this centrifugal pump is unreasonable.
Example No. 7
It is necessary to determine gear pump delivery coefficient. Pump geometrical characteristics: cross-sectional area of space between gear teeth is 720 mm2; number of teeth - 10; gear tooth length - 38 mm. Rotation speed is 280 rpm. Real gear pump delivery is 1.8 m3/h.
Solution:
Pump theoretical performance capacity is:
Q = 2·f·z·n·b = 2·720·10·0,38·280·1/(3600·106) = 0,0004256 m³/h
Correspondingly, delivery coefficient equals to:
ηV = 0,0004256/1,8·3600 = 0,85
Example No. 8
Pump having efficiency of 0.78 is pumping fluid with density of 1,030 kg/m3 and 132 m3/h flow rate. Head created in pipeline equals to 17.2 m. The pump is actuated by electric motor having power of 9.5 kW and efficiency of 0.95. It is necessary to determine whether this pump meets requirements in starting torque.
Solution:
We calculate useful power consumed directly for medium pumping:
NП = ρ·g·Q·H = 1030·9,81·132/3600·17,2 = 6372 W
We take into account efficiencies of pump and electric motor and determine full power requirements of electric motor:
NД = NП/(ηН·ηД) = 6372/(0,78·0,95) = 8599 W
As we know motor installed capacity, we determine power safety margin of the electric motor:
β = NУ/NД = 9500/8599 = 1,105
For motors with power from 5 to 50 kW it is recommended to select startup power margin from 1.2 to 1.15. The value we obtained does not fall within this interval, wherefrom one may conclude that in operation of this pump under set conditions problems can arise when starting it up.
Example No 9
Centrifugal pump is pumping fluid with density of 1,130 kg/m3 from open reservoir to reactor having operating pressure 1.5 bar and flow rate 5.6 m3/h. Geometrical difference of heads equals to 12 meters, with reactor installed below reservoir. Head friction losses in pipes and local resistances equal to 32. 6 m. Pump useful power has to be determined.
Solution:
We calculate the head created by pump in pipeline:
H = (p2-p1)/(ρ·g) + Hг + hп = ((1,5-1)·105)/(1130·9,81) - 12 + 32,6 = 25,11 m
Pump useful power can be found by the formula:
NП = ρ·g·Q·H = 1130·9,81·5,6/3600·25,11 = 433 W
Example No 10
We determine limiting increase of flow rate of water pumping (density is taken as equal to 1,000 kg/m3) from open reservoir to another open reservoir with flow rate of 24 m3/h. Geometrical head of fluid lift is 5 meters. Water is pumped along pipes 40 x 5 mm. Electric motor power is 1 kW. Total efficiency of the unit is taken as equal to 0.83. Total head friction losses in pipes and local resistances are 9.7 m.
Solution:
We determine maximal flow rate value corresponding to the maximum possible useful power developed by pump. To do this firstly we determine several intermediate parameters.
We calculate the head required for water pumping:
H = (p2-p1)/(ρ·g) + Hг + hп = ((1-1)·105)/(1000·9,81) + 5 + 9,7 = 14,7 m
Useful power developed by pump is:
NП = Nобщ/ηН = 1000/0,83 = 1205 W
We find maximal flow rate value from by formula:
NП = ρ·g·Q·H
We find sought quantity:
Qмакс = NП/(ρ·g·H) = 1205/(1000·9,81·14,7) = 0,00836 m³/s
Water flow rate can be increased 1.254 times at most without violation of pump operating requirements.
Qмакс/Q = 0,00836/24·3600 = 1,254